The eternal life of shrink hoods
26/02/2019Keep transport packaging as long as possible in circulation to improve their circularity. Discover how with "The eternal life of shrink hoods".
Valipac’s mission : facilitate the transition from a linear economy to a circular economy.
In early 2018, we set ourselves the goal of integrating transport packaging into a circular model. Our source of inspiration: Clean Site System, our system for collecting plastic film packaging on construction sites. In collaboration with the different actors in the value chain, the Clean Site Circular adventure had just begun. One year later, on February 15, 2019, the first shrink hoods were made from 50% recycled material.
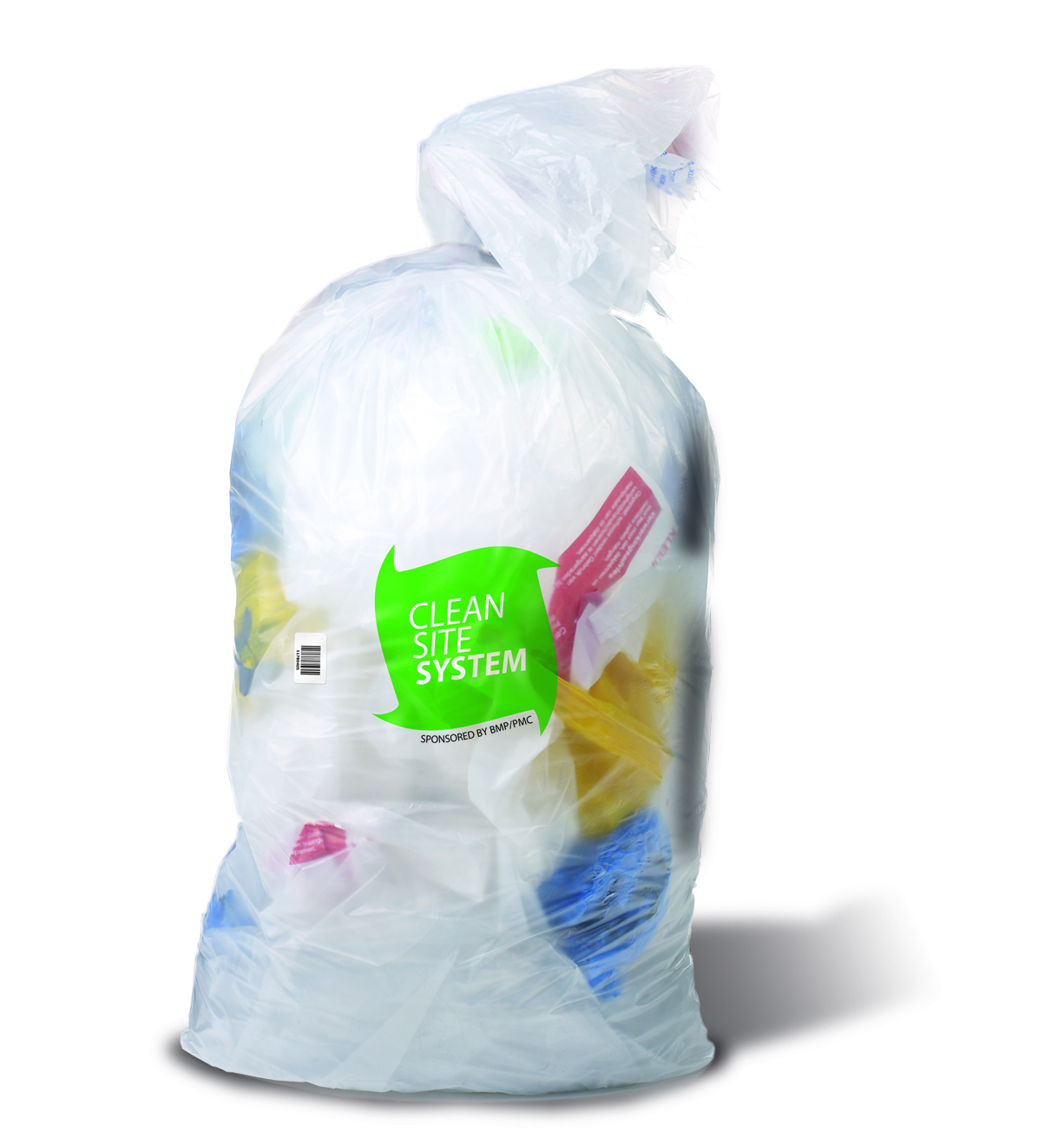
Clean Site System
Every year, more than 5.000 tonnes of plastic hoods reach construction sites. To prevent these plastics from ending up in an incinerator, Valipac developed in 2005 the Clean Site System. This system is based on reverse logistics. It offers the building contractors the opportunity to use bags to collect their plastic films on site and deposit them free of charge at their dealer. Today, about 6.000 contractors are using this service provided by 220 dealers in building materials located throughout Belgium.
This collection system is well anchored in the sector but could be further improved. These hoods are indeed made of virgin material. Valipac has therefore set itself the ambition of keeping these hoods longer in use.
For more info about the selective collection of plastics on construction sites have a look at our website Clean Site System
The construction industry, a source of inspiration
This ambition gave rise to a demonstration project : Clean Site Circular. Its purpose? To reinject the hoods used for the delivery of construction materials in the value chain by reusing the recycled content for the production of … new shrink hoods for the construction sector.
To achieve this project, we brought to the table partners who shared the same enthusiasm :
- Wienerberger, brick manufacturer, commited itself to using these circular shrink hoods provided that they have the same qualities as the hoods made from virgin material,
- Total developed the appropriate polymer mix that could be added to the regranulate produced by Rymoplast,
- Oerlemans manufactured the hoods from a mix of virgin polymers and regranulate.
- Fema and Go4Circle facilitated the contacts with the building material dealers and collectors/sorting centers.
For this project, Valipac and its partners have received financial support from Vlaanderen Circulair.
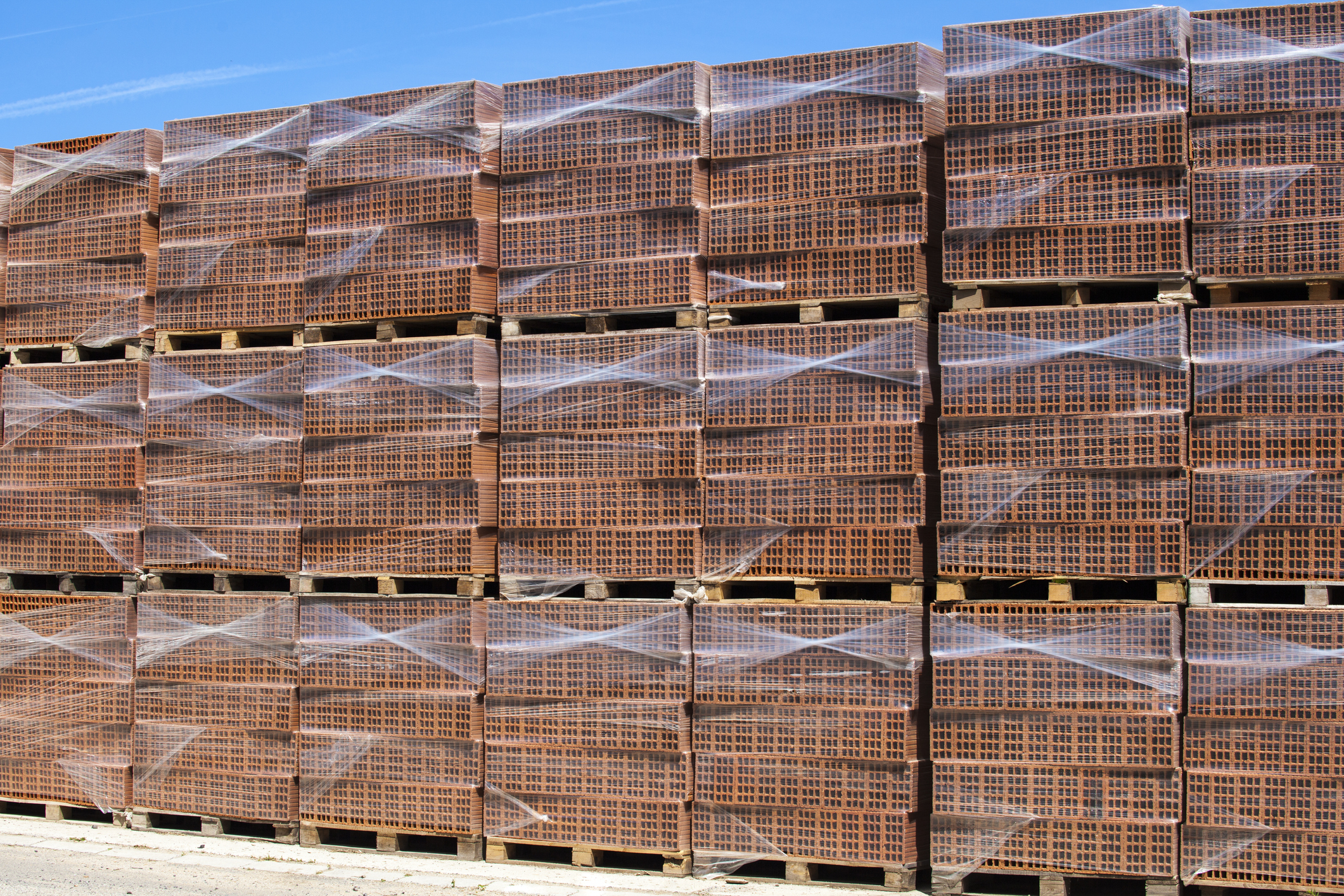
Design 4 Circularity
On February 15, Wienerberger used the very first circular shrink hoods to pack about ten pallets of bricks. These pallets have since passed succesfully the tests of compliance with European standards for transport safety.
The first results are promising but the project partners still want to continue the research. For example, they consider to increase the proportion of recycled content in the polymer mix or even to extend the tests to other qualities of regranulate.
This project has also highlighted the challenges of the current model: the use of ink or dyes reduces the circularity of the hoods as they increase the percentage of waste. Hence the need to define clear guidelines on the degree of recyclability of packaging to enhance their circularity.
Do circular shrink hoods have a future?
On February 26, Valipac was invited to participate in the prestigious World Resources Forum held in Antwerp. On this occasion, we organised a brainstorm session on the future of the circular shrink hoods.
As an introduction to this exchange of views, the partners presented the project to the audience. The participants were then divided into two working groups to give their opinion on two questions :
- What new economic model could improve the circularity of the shrink hoods ?
- How to maintain the balance between the recyclability of the hoods and the marketing aspect of printing ?
Each participant presented his ideas within the working group. All the ideas were then clustered and at a later stage, all participants were requested to cast a “preference vote”, each of them being able to retain three major ideas. At the end of these sessions, it soon became clear that both groups expect brand owners to get involved more actively and encourage the use of regranulate.
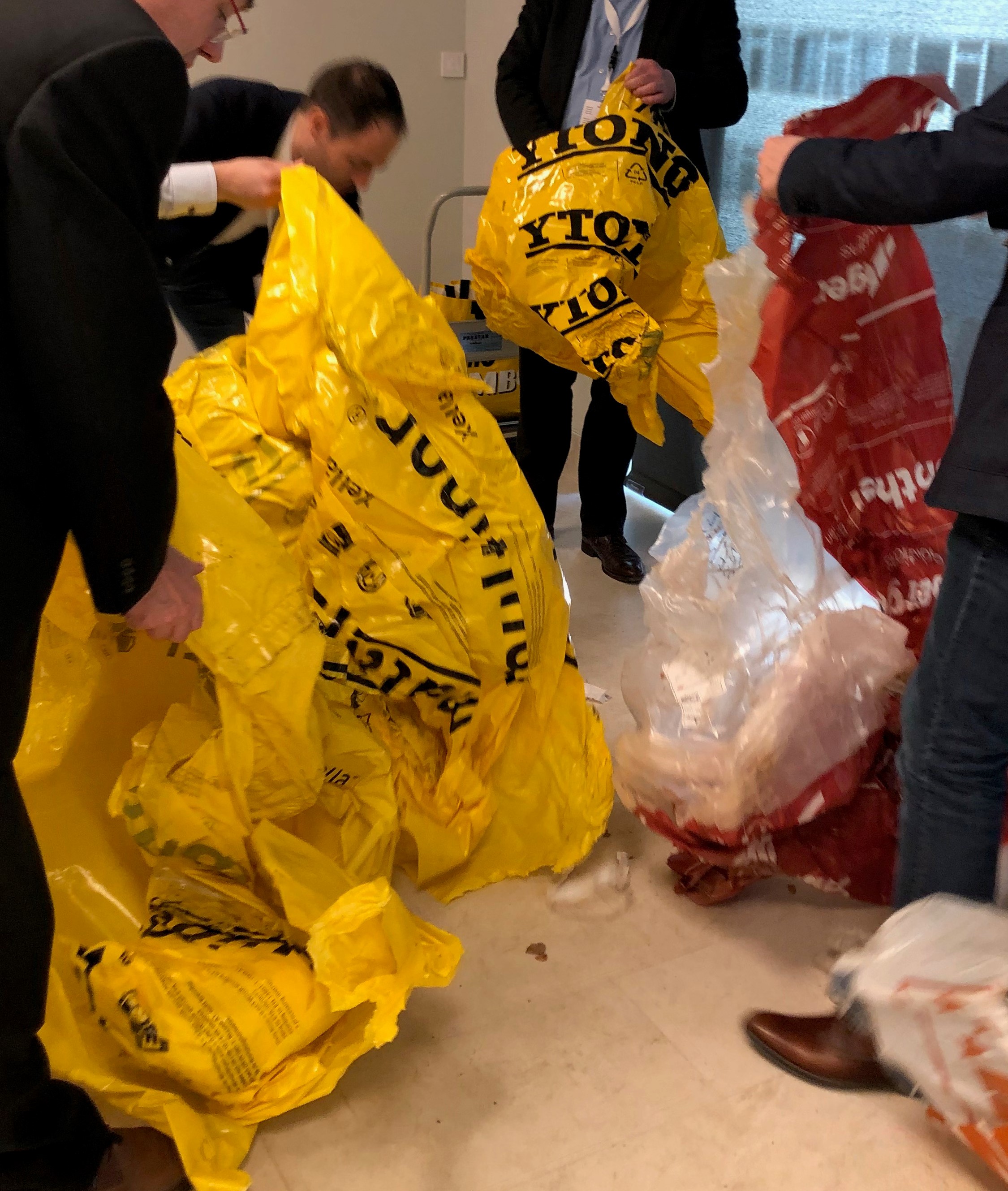
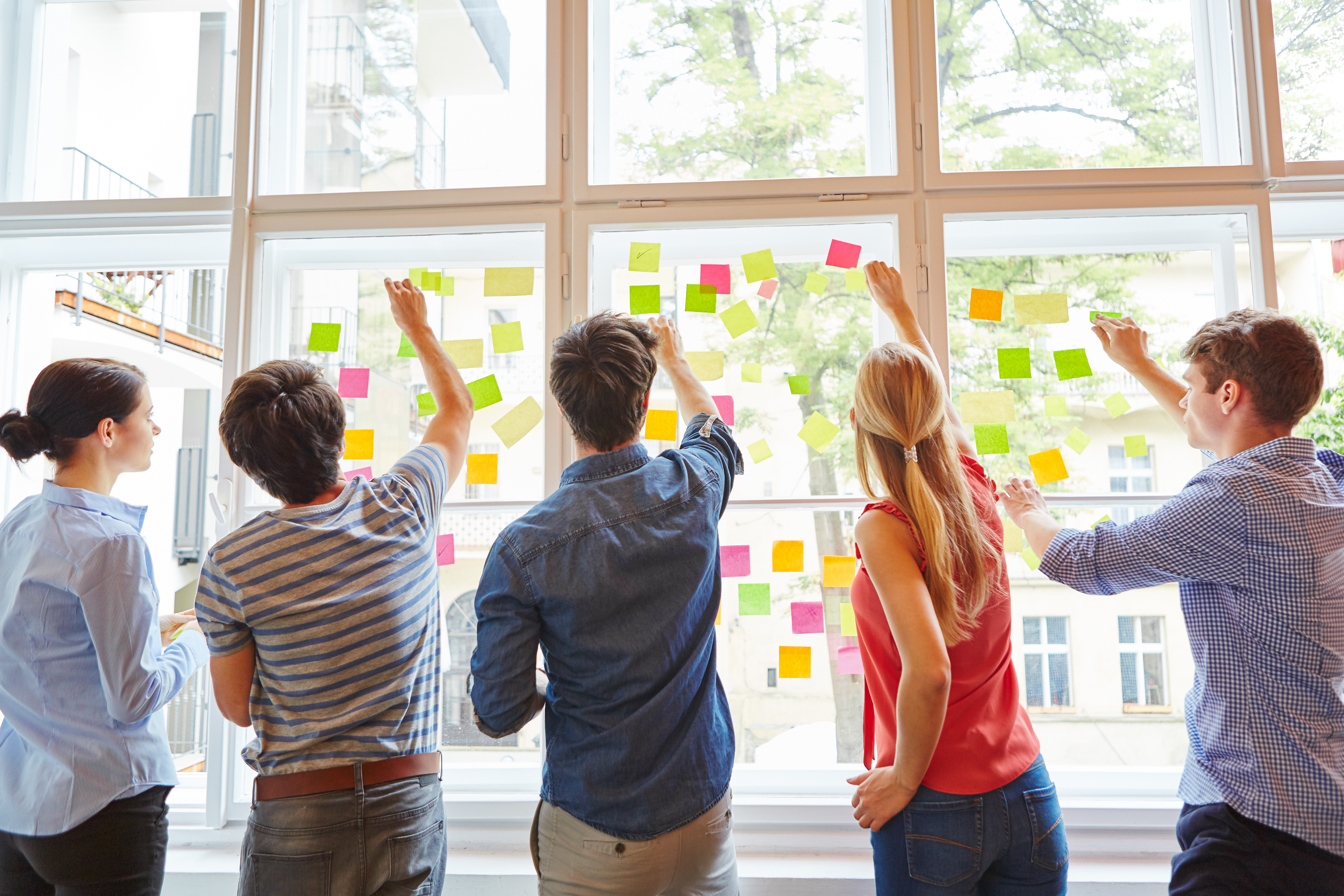
Results of the brainstorm session : The 3 best proposals made by each working group
Grey is the new virgin !
Group 1 : What new economic model could improve the circularity of the shrink hoods ?
- Authorities should be more actively involved in promoting the use of recycled materials in packaging. For example, they can have recourse to CO2 equivalent taxes, use eco-modulated rates applied by EPR organisations and any other measure that ensures that recycling is financially more beneficial than other forms of treatment,
- Recycling must be more efficient if we want to improve the quality of recycled materials and generate profits,
- Recyclers and virgin material suppliers need to cooperate more effectively and agree on well-defined product and quality specifications. This will help brand owners to better understand the market and increase their confidence in the use of regranulate.
Group 2 : How to maintain the balance between the recyclability of the hoods and the marketing aspect of printing ?
- Develop a special glue that allows the use of paper labels on the shrink hoods in order to keep the communication aspect. Ideally, this glue should dissolve during the wash cycle or melt at the same time as the polymer in the extruder,
- Have the greyish color of the hoods accepted by the brand owners,
- Develop a soluble ink or one that disappears after use. The ink may be removed by UV rays or under special conditions during the recycling process.
Valipac and its partners have proven the feasibility of this project. Our aim now, is to contact other sectors and try to convince them to join us in this adventure.
We want to thank all project partners for their enthusiasm and motivation.
For any information about this project, don’t hesitate to contact us at 02/456.83.10 or by e-mail at info@valipac.be